Development project about optimization of measurement processes
Siemens Gamesa uses photogrammetry for measurement of stators
Siemens Gamesa produces on- and offshore wind turbines, and with installations in more than 90 countries, the company is one of the world’s leading suppliers of wind power. Additionally, the global company is a key player within renewable energy.
Since 2012 Siemens Gamesa has used the metrology system TRITOP CMM for optical coordinate measurement of stators and flanges etc. Measurements which are used when producing large wind turbines without gears.
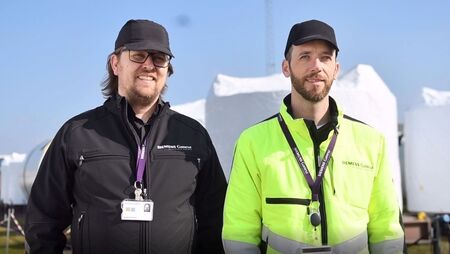
Production specialist Benjamin Henriksen (left) and production engineer Martin Bach Sørensen (right)
“What makes TRITOP an ideal system for us is that it is well suited for our production environment. In addition, the system has high accuracy, which is necessary for us to trust our measurements and know what we get out of our production.” - Martin Bach Sørensen, Production engineer at Siemens Gamesa
TRITOP CMM is a mobile and production friendly system, which is ideal for 3D measurements of large parts, and can be used on-site even under extreme conditions. The metrology system is based on photogrammetry, a technology that defines precise 3D positions on markers and visible elements.
In 2018 Siemens Gamesa went over several of its production processes to examine, which could be optimized and create better results.
Here the "marriage process", where rotor and stator are united, was chosen as a central process.
For a wind turbine generator, it is important that the stator and rotor are centered perfectly in relation to each other and create an even air gap in the generator.
The more accurate a center, the more power the wind turbine can produce, and the less thermal loss occurs. The result is less wear and tear and a longer lifespan for the generator.
For several years, Siemens Gamesa has measured the diameter of its stators and the center of flanges.
"We do this to make sure, that the product fits from the beginning, instead of finding out later that the air gap is uneven." - Martin Bach Sørensen
Earlier, this measurement process consisted of several manual processes, which required a thorough introduction. Furthermore, the result would vary depending on the operator, and as the operator subsequently had to enter many results manually, there was a risk of typing errors.
These were some of the challenges, which made Siemens Gamesa contact Zebicon to further develop the existing solution.
The purpose of the development project was to remove sources of variation, which could occur during measurement of the company's stators. Some wishes for the solution were: high precision, more user-friendliness, and automation of data processing.
"We have a great collaboration with Zebicon, who accepts the challenges and don't give up until they have found the right solution." - Martin Bach Sørensen
At first, Zebicon looked at how the stator's center was measured. Here the solution was a more simple setup, where the stators onwards would be measured in the same way, before and after the marriage process.
The project’s next step was to work with the user-friendliness. Today, the workflow is made as a guided measurement process, which helps the user from starting up the measurement, to finishing the inspection report. Thus, all operators can complete the measurement process with minimal introduction, which ensures more consistency in the measurement.
Furthermore, Zebicon has reworked the way to use measurement adapters. Adapters are used in combination with photogrammetry to recognize specific reference points, and based on these, determine a precise center.
The new adapters were developed with focus on mounting. It was imperative that they could not be turned upside down or be mounted in a wrong way. Additionally, the adapters should be precise and easy to handle.
The last part of the development project was about automating the data transfer and calculations.
”Today, we have an integrated system, where data automatically is sent to the next working process, where we cannot make any typing errors."
- Martin Bach Sørensen
The direct transfer of data means that there is no longer delay between the measurement station and the workstation where the stator and rotor is being united.
Siemens Gamesa is left with a measurement process, which has less variations and an increased accuracy in the measurement. This results in a faster production flow and, in the end, more powerful wind turbines.
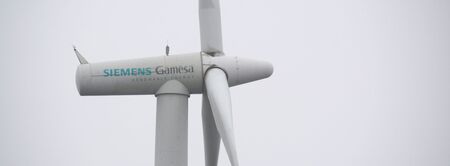
By refining the measurement process of stators, Siemens Gamesa has achieved optimization within serveral areas:
- Shorter measurement process
- Faster clarification about whether the part is approved or not
- Less variation in the measurement process
- Elimination of typing errors
- A more user-friendly workflow
- Minimal need for introduction and training
- Better data used for adjustments during the marriage process
Photogrammetry
Photogrammetry is optical 3D coordinate measurement. The technology is used for quality control of large parts, verification of fixtures and hand held tools as well as static deformation analysis.